Reduce Wear, Increase Efficiency
Friction Welding for Mining Components
Improve Machine Longevity and Reduce Wear
Mining equipment endures extreme conditions, including earth-shattering loads and brutal cold temperatures. With MTI’s unique friction welding process, your crew can maximize field time and minimize downtime in the repair shop.
MTI has been the global expert on friction welding technologies for 40 years. If you need to have a mining component designed and manufactured or have a friction welding machine in your production line, we have the resources and expertise to make it happen.
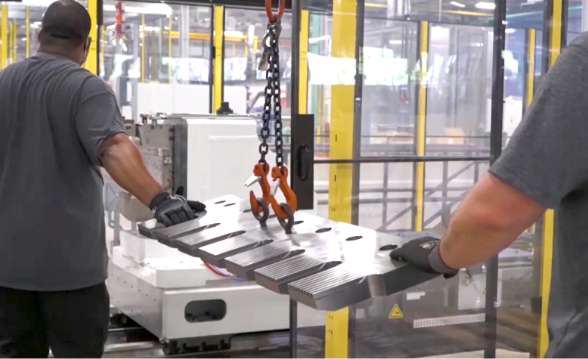
MTI employee loading parts into the LF35-75 Linear friction welding machine to be joined.
Advantages & Benefits
Forging Strength in Mining Operations
MTI’s friction welding solutions are revolutionizing the mining industry with unparalleled durability and performance. Our cutting-edge technologies deliver robust, long-lasting components that withstand the extreme conditions of mining operations, enhancing efficiency and reducing downtime.
Improved Tool Life
In a mining environment, equipment longevity and performance is vital to maintaining productive work. Because friction welding is a solid-state welding process, it minimizes the wear and tear on the equipment by avoiding high temperatures and thus, avoids the melting of materials. The joint durability allows for longer periods of continuous use, reducing downtime and maintenance costs
Stress-free Joints
Friction welding is a solid-state forging process. Materials being joined through friction welding are heated to a temperature that makes them plasticized, not melted. Then, using extremely high forces, the pieces are pressed together to form a forge quality bond. Since materials are not melted in the friction welding process, the result is a part featuring solid, 100% butt joints that are durable for years of use. Distortion is minimal and quality is consistent, leaving you with stress-free joints for years to come.
Reduce Wear
For years, oil sands companies have been brazing tungsten carbide tiles onto parts of their equipment that come into direct contact with the workload. While the tiles do, indeed, slow deterioration, it’s not a fail-proof method. Residual stress from thermal expansion and contraction causes a vulnerable condition at the edge of the brazed material. With friction welding, the process itself actually helps to decrease wear because of the low forging temperature.
Full-scale Parts
Ground engagement tools (GETs) used in the mining industry are typically large components used for heavy-duty work. MTI is home to the largest linear friction welder in the world. Weighing in at 122,000lbs with a measured size of 22’x8x14’, the LF35-75 supports your full-scale development and production goals.
In a mining environment, equipment longevity and performance is vital to maintaining productive work. Because friction welding is a solid-state welding process, it minimizes the wear and tear on the equipment by avoiding high temperatures and thus, avoids the melting of materials. The joint durability allows for longer periods of continuous use, reducing downtime and maintenance costs
Friction welding is a solid-state forging process. Materials being joined through friction welding are heated to a temperature that makes them plasticized, not melted. Then, using extremely high forces, the pieces are pressed together to form a forge quality bond. Since materials are not melted in the friction welding process, the result is a part featuring solid, 100% butt joints that are durable for years of use. Distortion is minimal and quality is consistent, leaving you with stress-free joints for years to come.
For years, oil sands companies have been brazing tungsten carbide tiles onto parts of their equipment that come into direct contact with the workload. While the tiles do, indeed, slow deterioration, it’s not a fail-proof method. Residual stress from thermal expansion and contraction causes a vulnerable condition at the edge of the brazed material. With friction welding, the process itself actually helps to decrease wear because of the low forging temperature.
Ground engagement tools (GETs) used in the mining industry are typically large components used for heavy-duty work. MTI is home to the largest linear friction welder in the world. Weighing in at 122,000lbs with a measured size of 22’x8x14’, the LF35-75 supports your full-scale development and production goals.
Our Commitment
Quality First, Every Time
MTI brings the highest possible degree of safety and quality, whether it’s a part we’re welding or a machine we’re building. We are equipped to produce parts for the most sensitive environments and exacting standards.
Friction Welding Machines for the Mining Industry
MTI-built friction welding machines handle large and small mining components with precision and reliable quality. Trusted worldwide, our machines continue to operate efficiently, meeting the demanding standards of the mining industry.
Friction Welding Machines for the Mining Industry
MTI-built friction welding machines handle large and small mining components with precision and reliable quality. Trusted worldwide, our machines continue to operate efficiently, meeting the demanding standards of the mining industry.
ROTARY FRICTION WELDING
Custom Rotary machines have been produced and supplied by MTI across the globe.
LOW FORCE FRICTION WELDING
MTI’s Low Force friction welding results in a smooth flash with minimal upset.
LINEAR FRICTION WELDING
Build the largest full-scale bimetallic mining components with MTI-built LF35-75.
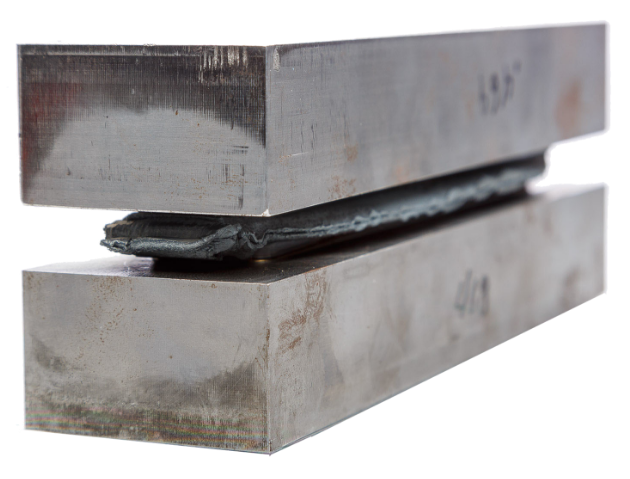
Explore Our Sample Parts
Discover our range of high-performance friction welded components designed specifically for the mining industry, including durable ground engagement tools, impact hammers, and grader edges. We are committed to providing robust solutions for even the most demanding mining applications.
Contract Manufacturing Services
From consultation to testing, manufacturing, maintenance, and personnel training, MTI covers every aspect. Complete your mining project seamlessly with us by designing and building friction welding machines or mining components in one place.
Contract Manufacturing Services
From consultation to testing, manufacturing, maintenance, and personnel training, MTI covers every aspect. Complete your mining project seamlessly with us by designing and building friction welding machines or mining components in one place.
Mining Friction Welding Machines for R&D
Make Your Mining Innovation Happen
MTI has in-house friction welding machines to meet your research and development needs. Explore and innovate with various materials and applications for ground engagement tools and impact hammers.
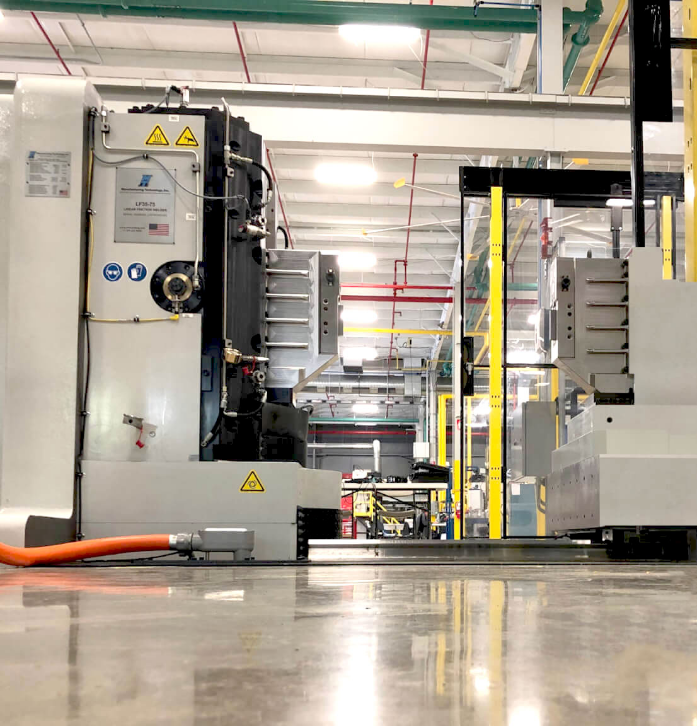
A closer look at MTI’s LF35-75 Linear friction welding machine capable of full-scale part development and production.
Learning Center
Featured Articles
Case Studies
Videos
Get the information you need, before you need it — free and straight to your inbox from industry experts.