Wheels Up
Friction Welding for Aerospace and Aircraft Components
MTI Meets the Constantly Changing Needs of the Aerospace Industry
MTI has worked for decades with high-profile aerospace companies to develop new, innovative parts. Our skilled engineers can walk you through the research and development process to pinpoint your exact needs and bring them to life. We can build a machine to make your part, make your part for you, or help make your part better.
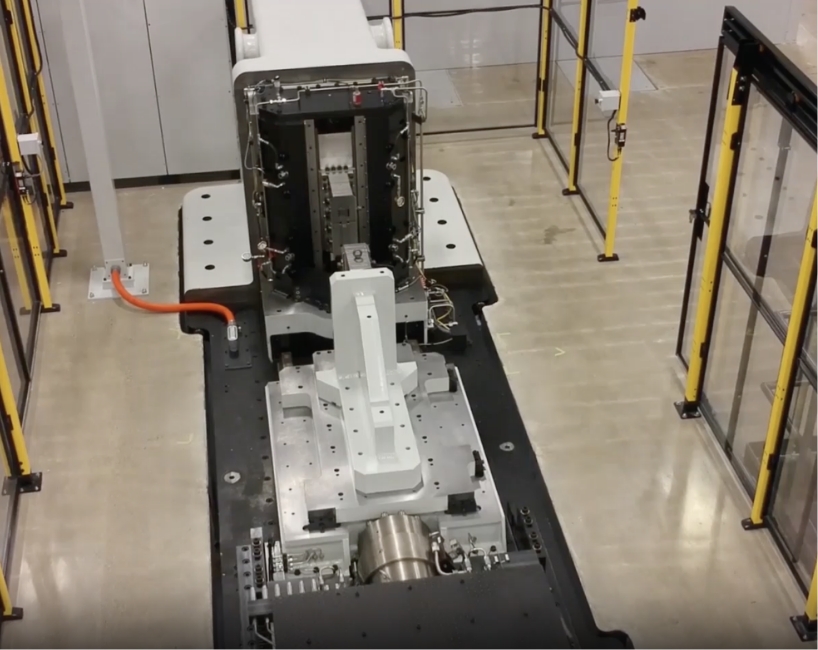
MTI’s LF35-75 Linear friction welding machine available to join full-scale components.
Advantages & Benefits
Soaring to New Heights in Aerospace Engineering
MTI’s advanced friction welding technologies are propelling the aerospace industry forward. Our innovative solutions offer key advantages that optimize aircraft performance, reduce operational costs, and push the boundaries of aerospace manufacturing.
(Tailored/Close Contour Blanks)
Cut MRO Costs
Cut MRO (Maintenance, Repair, and Operations) costs for aerospace companies with Friction Welding as it provides a strong, reliable joint without the need for additional materials like adhesives or fasteners. This process minimizes material waste and reduces the time required for repairs, leading to lower labor costs. Additionally, the improved joint integrity and durability enhance the lifespan of components, resulting in less frequent maintenance.
Lightweighting
Friction Welding opens the door to joining of dissimilar materials, which allows designers to use lighter and/or higher performance materials than traditional joining methods. This allows for reduced weight of parts — and ultimately, better fuel efficiency. These advanced materials require the use of Friction Welding.
Near-Net Shape Joining (Tailored/Close Contour Blanks)
“Near-net shape” components can be created through Linear or Rotary Friction Welding, requiring minimal additional machining, saving costly time and materials. Airframe structures and blisks used in jet engine assemblies are two examples of parts created through near-net shape joining.
Cut MRO (Maintenance, Repair, and Operations) costs for aerospace companies with Friction Welding as it provides a strong, reliable joint without the need for additional materials like adhesives or fasteners. This process minimizes material waste and reduces the time required for repairs, leading to lower labor costs. Additionally, the improved joint integrity and durability enhance the lifespan of components, resulting in less frequent maintenance.
Friction Welding opens the door to joining of dissimilar materials, which allows designers to use lighter and/or higher performance materials than traditional joining methods. This allows for reduced weight of parts — and ultimately, better fuel efficiency. These advanced materials require the use of Friction Welding.
"Near-net shape” components can be created through Linear or Rotary Friction Welding, requiring minimal additional machining, saving costly time and materials. Airframe structures and blisks used in jet engine assemblies are two examples of parts created through near-net shape joining.
Our Commitment
Quality is at the core of our ingenuity
MTI brings the highest possible degree of safety and quality, whether it’s a part we’re welding or a machine we’re building. We are equipped to produce parts for the most sensitive environments and exacting standards.
Friction Welding Machines for Aerospace
Friction welding machines designed with the aerospace industry in mind. Explore the capabilities and possibilities of MTI’s line of aerospace friction welders.
Our Model 400 is the world’s largest Inertia Friction Welder for contract manufacturing. See it in action.
Friction Welding Machines for Aerospace
Friction welding machines designed with the aerospace industry in mind. Explore the capabilities and possibilities of MTI’s line of aerospace friction welders.
Our Model 400 is the World’s Largest Inertia Friction Welder for Contract Manufacturing. See it in Action.
ROTARY FRICTION WELDING
All mainstream aerospace engine manufacturers utilize and trust MTI-build friction welders for the critical components.
LOW FORCE FRICTION WELDING
MTI is the only company in the world to have developed and designed Low Force Friction Welding machines operating in production today.
LINEAR FRICTION WELDING
MTI is the leading manufacturer to have multiple Linear Friction Welding machines in operation around the globe.
FRICTION STIR WELDING
This solid-state process is ideal for air and space travel because of its lightweighting capabilities and increased strength in the weld seams.
PLUG WELDING
A unique form of friction welding specifically designed to help aerospace companies save on MRO costs.
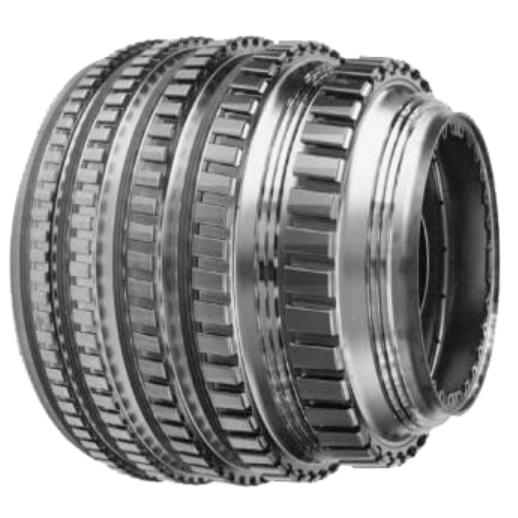
Explore Our Sample Parts
View Our sample friction welded parts catalog to uncover applications that might be right for your next project.
Contract Manufacturing Services
We don’t just build friction welders – we operate them, too. When you partner with any of our global Contract Friction Welding teams, we will handle your project from start to finish on our state-of-the-art friction welding machines. Whether you need one part every year or one part every minute, we are here to help you reach your production goals across the globe.
Contract Manufacturing Services
We don’t just build friction welders – we operate them, too. When you partner with any of our global Contract Friction Welding teams, we will handle your project from start to finish on our state-of-the-art friction welding machines. Whether you need one part every year or one part every minute, we are here to help you reach your production goals across the globe.
Aerospace Friction Welding Machines for R&D
Test your materials and applications on MTI’s line of in-house R&D machines.
R&D is a necessary step in the friction welding process for joining bimetallics, designer materials such as powdered metals, and other exotic materials. MTI has several machines in-house that are ready to be utilized for testing in your next project.
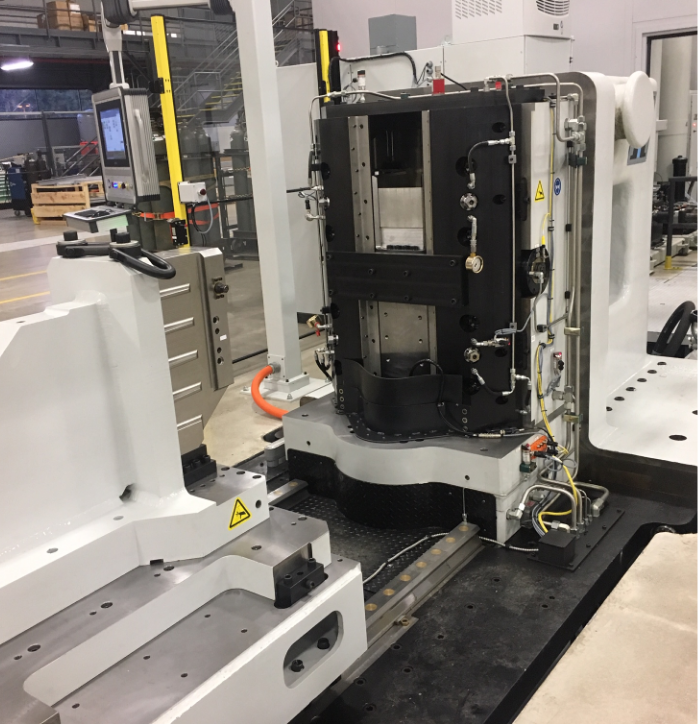
Learning Center
Featured Articles
Case Studies
Videos
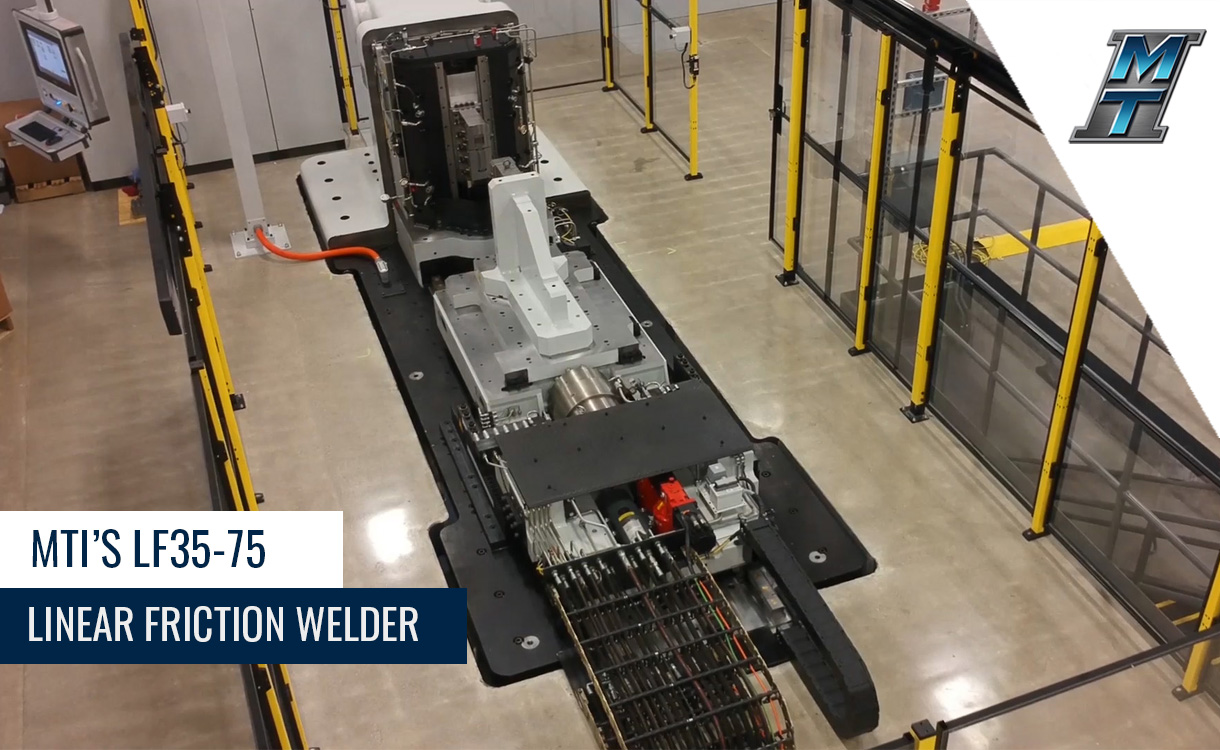
Aerospace Video
Get the information you need, before you need it — free and straight to your inbox from industry experts.