Automated Welding
Improve productivity with automated friction welding
Welding Automation
At MTI, we aim to provide the next generation of autonomous integrated welding systems, leveraging our world-class process knowledge and the latest technology. Focusing on customized, low-risk configurations, we design and build a range of semi- or fully automated friction welding machines tailored to requirements that deliver enhanced quality, productivity, and ROI.
Our automated welding services include robotic systems where welding robots execute motions based on a predetermined script or training from a robot controller. A robot welder works tirelessly without fatigue, resulting in earlier project completion times. These automated systems can save labor, costs, and other resources in varied industries.
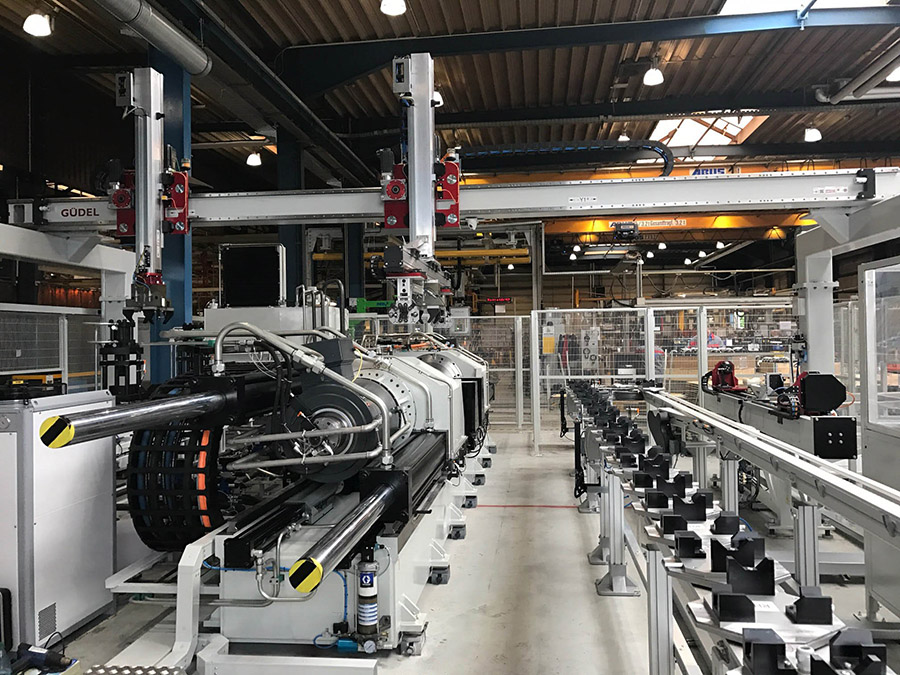
MTI’s machine design and build services extend to include semi or fully automated cells to meet your needs.
Advantages & Benefits
Automated Welding Processes: Automating Through Robotic Welding
At MTI, we offer semi-automated and fully automated friction welding machine solutions, integrating a combination of advanced robotic and gantry systems. Here are just a few of benefits to automated welding:
Improve Weld Quality
Automated welding machines ensure weld integrity through electronic weld process controllers. With a combination of mechanized torque, part motions, and electronic recall of welding parameters, the automation results in a higher-quality weld.
Control Quality In-Line
An automated machine makes a weld only once, so material defects are readily visible and detectable. Human welders may try to fix the mistake, possibly concealing a flawed weld. Leak testing and vision systems can sometimes be integrated into fully automated welding processes to provide additional in-line quality control
Increase Work Productivity
A fully automatic system can comprise twin welding positioners on an automated shuttle. This system can load and unload parts at one station while welding occurs at another. With this type of full automation setup, a system can run up to 4X faster than a semi-automatic welding process or 8X faster than a skilled welder.
Better Utilization of Resources
A facility can automate in hazardous areas or under harsh conditions that might compromise the safety of a human operator. Furthermore, automation reduces the risk of accidents and improves performance. Automated welding machines can undertake highly repetitive tasks, freeing employees to work on tasks requiring more expertise. This mechanized automation results in a better ROI for the business while potentially improving employee satisfaction.
Reduce Waste
An automation system enables organizations to minimize different types of waste in their facility, such as closer equipment placement to minimize the space needed in a facility. Automation also provides repeatable input parameters for more repeatable output, leading to reductions in both waste and rework on components, which reduce the risk of damage or breakage due to incorrect handling.
Maximize Efficiency
Automated welding production speeds are set at a percentage of maximum by the machine instead of an operator. With minimal setup time and faster weld speeds, an automated welding system can easily outpace a skilled manual welder.
Automated welding machines ensure weld integrity through electronic weld process controllers. With a combination of mechanized torque, part motions, and electronic recall of welding parameters, the automation results in a higher-quality weld.
An automated machine makes a weld only once, so material defects are readily visible and detectable. Human welders may try to fix the mistake, possibly concealing a flawed weld. Leak testing and vision systems can sometimes be integrated into fully automated welding processes to provide additional in-line quality control
A fully automatic system can comprise twin welding positioners on an automated shuttle. This system can load and unload parts at one station while welding occurs at another. With this type of full automation setup, a system can run up to 4X faster than a semi-automatic welding process or 8X faster than a skilled welder.
A facility can automate in hazardous areas or under harsh conditions that might compromise the safety of a human operator. Furthermore, automation reduces the risk of accidents and improves performance. Automated welding machines can undertake highly repetitive tasks, freeing employees to work on tasks requiring more expertise. This mechanized automation results in a better ROI for the business while potentially improving employee satisfaction.
An automation system enables organizations to minimize different types of waste in their facility, such as closer equipment placement to minimize the space needed in a facility. Automation also provides repeatable input parameters for more repeatable output, leading to reductions in both waste and rework on components, which reduce the risk of damage or breakage due to incorrect handling.
Automated welding production speeds are set at a percentage of maximum by the machine instead of an operator. With minimal setup time and faster weld speeds, an automated welding system can easily outpace a skilled manual welder.
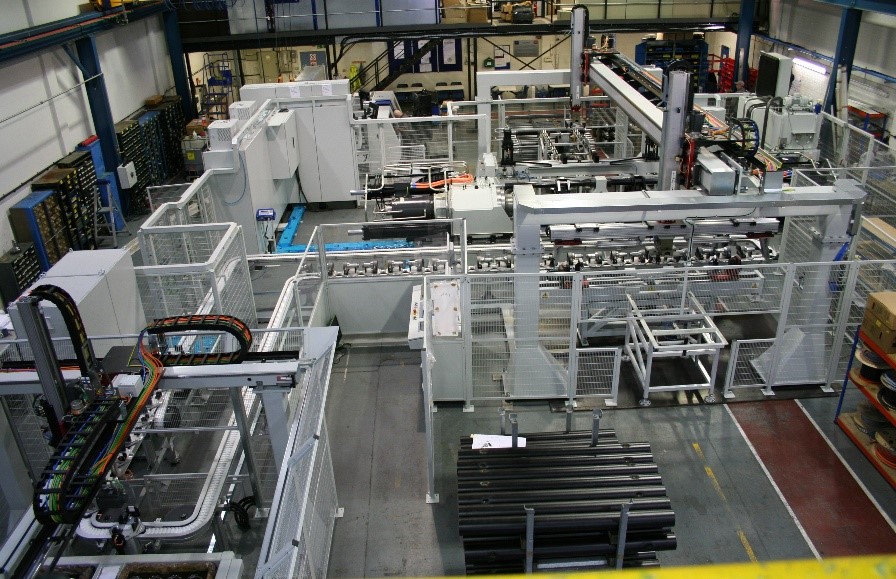
The Robotic Welding Process
We pride ourselves on designing and manufacturing automated friction welding machines tailored to your specifications and preferences. Should you have a preferred automation or robotic automation supplier, we seamlessly integrate these into the machine cell to enhance weld quality, boost productivity, and minimize defects.
Robotic Welding: The robotic automation of the welding process is ideal for complex and precise weld lines. It utilizes a multi-axis robot arm to achieve exceptional accuracy. A robotic welder is also suitable for welding inaccessible locations.
Gantry Welding: Perfect for applications requiring linear movements, such as loading and unloading systems, our gantry welding solutions ensure efficiency and reliability.
Get the information you need, before you need it — free and straight to your inbox from industry experts.